Big Data und Analytics findet Einzug in der industriellen Fertigung. Erfahren Sie, welche Learnings ein Schweizer Medizintechnik-Unternehmen in einem ersten Pilotprojekt gemacht hat. Ein Wirtschaftsinformatik-Student berichtet aus seinen Erfahrungen.
Die Ypsomed ist Herstellerin von Pen-Systemen für Pharmaunternehmen, sowie Insulin-Pumpen für intensiv therapierte Diabetiker. Sie verfügt über Produktionswerke in der Schweiz und Norddeutschland, wo sie über 120 Kunststoffspritzguss-Maschinen und mehrere hochautomatisierte Montage-, Bedruckungs- und Verpackungsanlagen einsetzt.
Von der Ausgangslage zum Projekt
Wie viele Unternehmen investiert auch die Ypsomed seit Jahren stark in die Digitalisierung und Automatisierung von Prozessen. Dadurch werden bereits heute sehr viele Daten erzeugt und stehen grundsätzlich zur Verfügung. Ein Raumüberwachungssystem zeichnet die Luftkondition auf. Messsysteme messen Qualitätskriterien an produzierten Teilen. Maschinen in der Produktion generieren Prozess- und Sensordaten zur Steuerung ihrer eigenen Arbeitsabläufen. Jedoch werden insbesondere Daten aus den Fertigungsprozessen noch nicht für weitere Zwecke vorgehalten, und wenn doch, dann in unterschiedlichsten Daten-Silos.
Aufgrund dieser Ausgangslage setzte sich ein Projektteam vor etwa zwei Jahren zusammen und stellte sich die Fragen: Welchen Nutzen kann gezogen werden, wenn all diese Daten prozess- und systemübergreifend abgegriffen, kombiniert und aggregiert werden können? Was für Anwendungsfälle würden sich aus einem zentralen Datenpool entwickeln? Man entschied sich dazu, zusammen mit einem externen Spezialisten, die Vision einer ganzheitlichen Analytics- und Big-Data-Plattform für das Unternehmen zu entwickeln und ein erstes Pilotprojekt umzusetzen. Nach einer umfangreichen Konzeptionierungsphase mit mehreren Workshops mit Teams aus der IT und der Produktion, baute man innerhalb von rund zwölf Monaten einen Hadoop-Cluster auf und setzte erste Anwendungsfälle um.
Ein kurzes Einführungsvideo zu Big Data und Industrie 4.0 (Quelle: Youtube):
Die wichtigsten Erkenntnisse aus dem Pilotprojekt werden nun etwas genauer beleuchtet.
Learning #1 – Picking the low-hanging fruits
Bei der Auswahl der ersten Anwendungsfällen kann es sinnvoll sein, solche zu selektieren, welche rasch umgesetzt werden können und schnell einen Mehrwert generieren. Idealerweise wählt man hierzu Szenarien, wo das Unternehmen bereits über ein grosses internes Knowhow verfügt und welche nicht über eine zu grosse Komplexität verfügen. Beispielsweise:
Shopfloor-Visualisierungen
Dashboards stellen aktuelle prozess- und qualitätsrelevante Sensordaten sowie berechnete Kennzahlen in der Produktion dar. Durch diese prozessnahe Visualisierung sind Mitarbeitende besser über den Zustand ihrer Produktionsstrassen informiert und haben schnellere Reaktionsmöglichkeiten auf Veränderungen. Eine effektivere Einflussnahme auf Produktionsprozesse ist möglich.
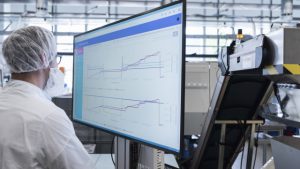
Automatisierte und standardisierte Qualitätsberichte
Als Produzentin in der Medizintechnik ist die Ypsomed verpflichtet, jederzeit aufzeigen zu können, dass eine produzierte Teile zu den vorgegebenen Bedingungen produziert wurden. Nach Abschluss der Fertigungsaufträge im ERP-System werden über die verschiedenen Produktionen hinweg standardisiert und automatisiert Qualitätsberichte generiert und archiviert. Diese Berichte verfügen über Qualitätsinformationen, aggregiert aus aufgezeichneten Sensordaten.
Retrospektive Maschinendaten-Analysen
Durch das Aufzeichnen von unterschiedlichen Produktionsparameter über eine längere Zeit hinweg, können diese nun analysiert und verglichen werden. Ein konkretes Beispiel: In der Spritzguss-Fertigung kann ein Temperaturverlauf einer Spritzgussmaschine im Vergleich zur Maschinenlaufzeit interessante Hinweise geben. Durch die graphische Aufbereitung können Anomalien leichter erkannt werden und die Produktion erhält einen neuen «Lern-Kanal» um mehr über ihre Prozesse in Erfahrung zu bringen.
Learning #2 – Spezialisten dazu ziehen und Knowhow aufbauen
Während der Konzeptionierung wurde dem Projektteam bewusst, dass es keine passende Standard-Lösungen „out-of-the-box“ gibt. Ein Unternehmen muss selbst herausfinden, welches Vorgehen und welche Lösungen sich am besten eignen. An dieser Stelle hilft einerseits, dass man gute Partnerschaften mit Experten auf dem Gebiet aufbaut und pflegt. Andererseits erkannte man auch, dass intern notwendiges Knowhow angeeignet und aufgebaut werden muss. Nur so können Diskussionen auf Augenhöhe mit Spezialisten-Teams geführt und optimale Lösungen entwickelt werden.
Learning #3 – Schnittstellen standardisieren
Ein Problem, mit welchem man stark konfrontiert wurde, ist die riesige Schnittstellen-Vielfalt im Maschinenpark. In den verschiedenen Produktionen haben sich über die Jahre unterschiedlichste Maschinen-Typen und –Modelle angesammelt, welche je nach Baujahr wiederum über zusätzliche Schnittstellen-Typen verfügen. Um an die benötigten Maschinendaten zu gelangen, ist eine so weit als mögliche Standardisierung der Maschinen-Anbindung sehr wichtig.
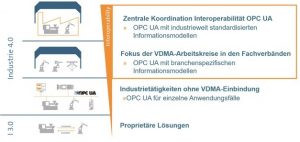
Learning #4 – Raum für Innovation schaffen
Und zu guter Letzt: Man muss versuchen mutig zu sein! Mutig sein, um Dinge auszuprobieren, wo man zwar weiss, dass die Richtung stimmt, aber das Resultat noch nicht wirklich greifbar ist. Mutig sein, um neben der täglichen Arbeit Freiräume für Innovation zu schaffen. Und man sollte akzeptieren, dass man hin und wieder eine Bauchlandung hinlegt. Wichtig ist nur, dass man vorwärtsfällt und dabei wiederum mindestens einen Schritt vorwärtskommt.
Weitere Links zum Thema: